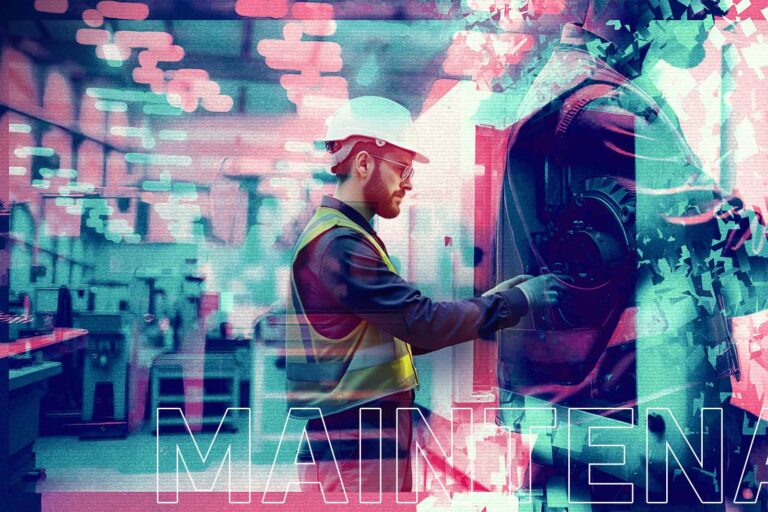
Reactive maintenance: What is it and when does it make sense to use it?
Reactive maintenance, often called “post-failure repair,” is a maintenance strategy where the equipment is only repaired when it fails. Unlike preventive or predictive maintenance, the reactive approach